VALVES
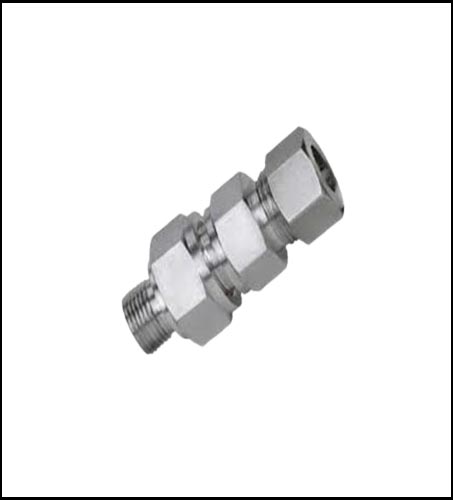
Non – Return Valve
Check valves are often used with some types of pumps. Piston-driven and diaphragm pumps such as metering pumps and pumps for chromatography commonly use inlet and outlet ball check valves. These valves often look like small cylinders attached to the pump head on the inlet and outlet lines. Many similar pump-like mechanisms for moving volumes of fluids around use check valves such as ball check valves. The feed pumps or injectors which supply water to steam boilers are fitted with check valves to prevent back-flow. Check valves are used in many fluid systems such as those in chemical and power plants, and in many other industrial processes.
Check valves are also often used when multiple gases are mixed into one gas stream. A check valve is installed on each of the individual gas streams to prevent mixing of the gases in the original source. For example, if a fuel and an oxidizer are to be mixed, then check valves will normally be used on both the fuel and oxidizer sources to ensure that the original gas cylinders remain pure and therefore nonflammable
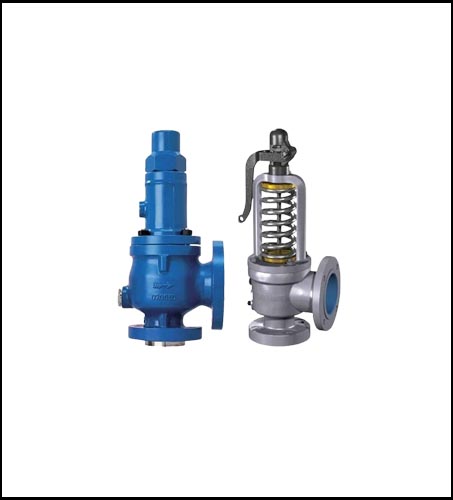
Pressure Relief Valve
It is a type of valve use to control or limit the pressure in a vessel which can build up by a process upset, instrument or equipment failure

Flush Bottom Drain Valve
This Valve is used to drain out the material from the Autoclave. Nearly no dead-space has been realized by the special design of the valve. This valve can be easily screwed out of the autoclave for repairs and maintenance.
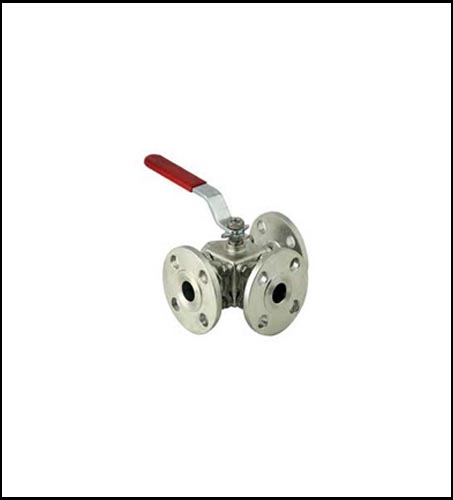
Ball Valves
Ball valves are used extensively in industrial applications because they are very versatile, supporting pressures up to 1000 bars and temperatures up to 482°F (250°C). Sizes typically range from 0.2 to 11.81 inches (0.5 cm to 30 cm).
They are easy to repair and operate.The body of ball valves may be made of SS 304. The ball is often chrome plated to make it more durable. Ball valves are durable and usually work to achieve perfect shutoff even after years of disuse. They are therefore an excellent choice for shutoff applications. They do not offer the fine control that may be necessary in throttling applications.
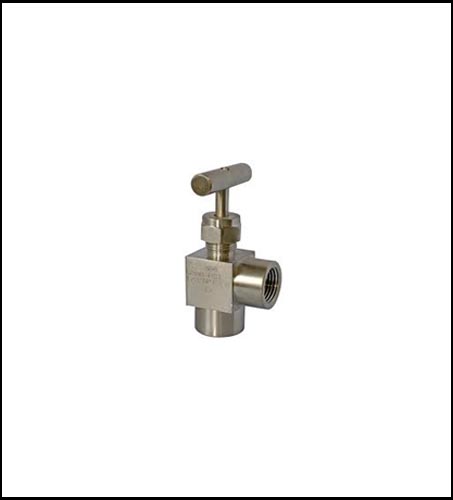
Angled Needle Valves
Needle valves are usually used in flow metering applications, especially when a constant, calibrated, low flow rate must be maintained for some time. A needle valve has a relatively small orifice with a long, tapered seat, and a needle-shaped plunger, on the end of a screw, which exactly fits this seat.
As the screw is turned and the plunger retracted, flow between the seat and the plunger is possible; however, until the plunger is completely retracted the fluid flow is significantly impeded. Since it takes many turns of the fine-threaded screw to retract the plunger, precise regulation of the flow rate is possible.
The virtue of the needle valve is from the vernier effect of the ratio between the needle's length and its diameter, or the difference in diameter between needle and seat. A long travel axially (the control input) makes for a very small and precise change radially (affecting the resultant flow). Needle valves may be used in vacuum systems, when a very precise control of gas flow is required, at low pressure.